Committed to providing efficient and cost-effective handling solutions for dry bulk cargo transported within East Africa, we speak with Jared Locklear, Chief Operating Officer of Grain Bulk Handlers Limited.
INTRODUCTION
As a whole, Africa is a diverse and rapidly evolving market. There are 54 unique and amazing countries across the continent that each have their own policies, level of infrastructure development, acceptance, and utilisation of technologies along with cultural nuances.
With the advent of the African Continental Free Trade Area (AfCFTA), in addition to the various regional trading blocs, the continent and the leaders of these countries are working in a very positive transformational direction.
“There is still a lot of work to be done regarding the coordination of policies and execution of the works, but the job has commenced, and we look forward to the changes in the coming years that will enable greater free trade across the various regions and the continent as a whole,” opens Jared Locklear, Chief Operating Officer for Grain Bulk Handlers Limited (GBHL).
The continent finds itself at a pivotal point with growth across all sectors, and GBHL is proud to be a part of that today and in the coming years and decades.
“Africa is an amazing environment to work in and there are increasingly more organisations, such as ours, that are driving innovation in processes and systems, streamlining operations, and implementing technology to create efficiency that can help to enable the reduction in the cost of goods and services and to ultimately create jobs and empower consumers,” he continues.
GBHL is a private company which commenced operations in 2000. It owns and operates a specialised terminal for the handling of dry bulk imports at the Port of Mombasa, Kenya.
A key feature of the GBHL facility is that the storage silos and flat storage are located outside the port area, allowing for easy terminal access for trucks with minimum road congestion.
Impressively, the total storage capacity is 220,000 metric tons (MT) for grains, 65,000 MT for fertiliser and 120,000 MT for clinker, with a discharge rate of a maximum of 1,800 MT per hour and capacity for over 20,000 MT per day.
The terminal has bagging and bulk loading facilities for rail and road together with weighbridges, whilst conventional bulk vessel operations are less efficient and vessels often have to wait, hence the waiting time and demurrage are not deemed economical.
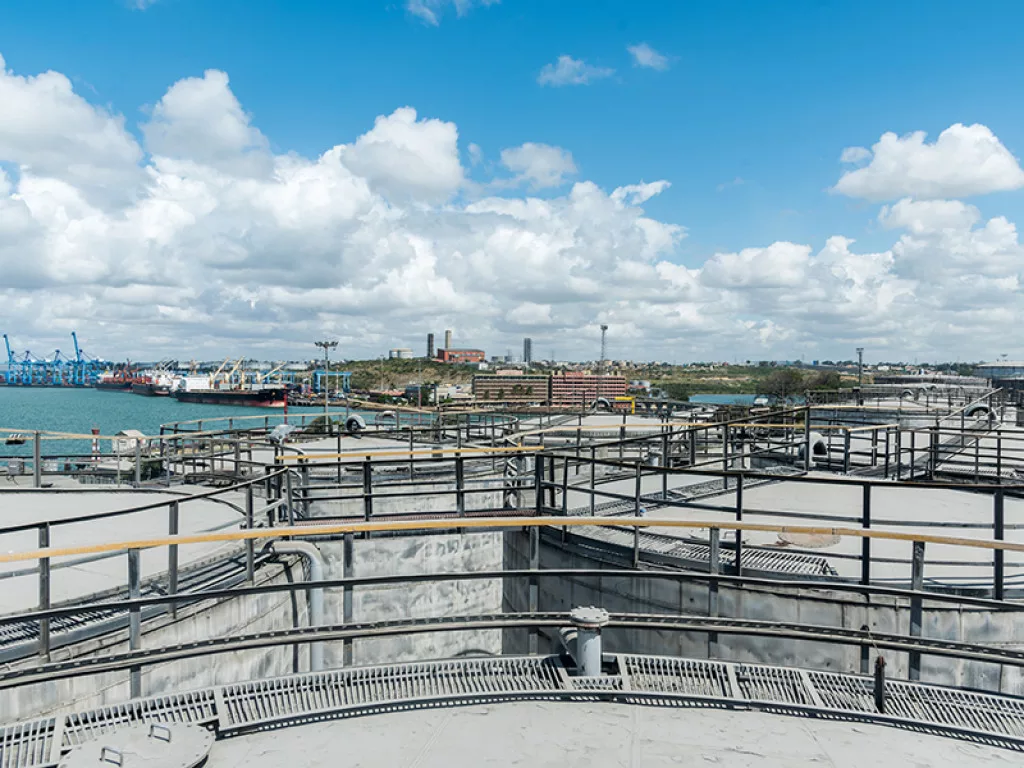
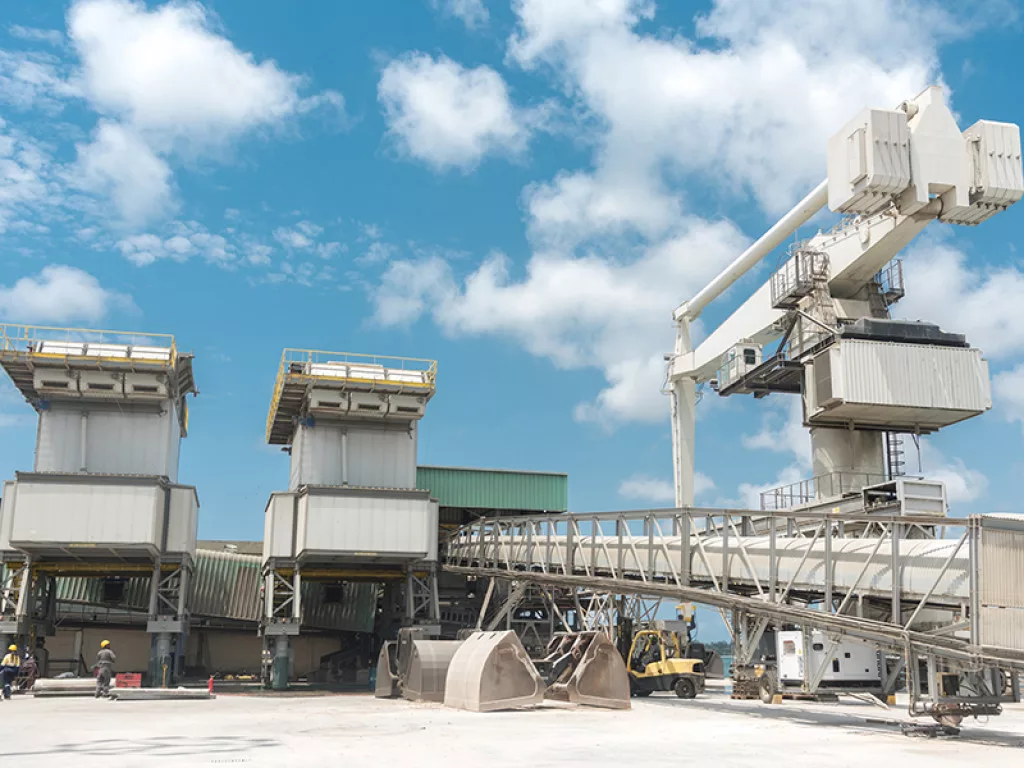
LOGISTICS SOLUTIONS FOR THE REGION
Today, GBHL employs over 500 permanent staff and nearly 500 casual workers across its various operations in Kenya and Uganda, handling vessel offloading at the Port of Mombasa for cereals, clinker, and fertiliser.
Elsewhere, GBHL designs, constructs, and owns the intellectual property for specialised containers that are used to transport bulk and bagged cargo from its terminals in Mombasa to the terminals in Embakasi and Jinja, through the utilisation of the Standard Gauge Railway (SGR) operated by Kenya Railways, and through the Meter Gauge Railway (MGR) connection in Naivasha. This allows the company to interchange its containers for the delivery of cargo to the terminal in Jinja.
“We serve over 50 major industrial customers across the region with our logistics solutions across the full spectrum of bulk commodities that are imported through the Port of Mombasa,” Locklear tells us.
“We have grown from handling just over 400,000 MT of cargo in our first year to now handling over 5.4 million MT per annum.
“We are a highly driven organisation with leadership that is keen on utilising technology and innovation to create economically sustainable solutions for our customers, therefore directly leading to savings in the logistics supply chain while achieving the highest level of performance for their needs,” he expands.
A major project milestone for GBHL was the recent commissioning in May 2022 of a new terminal in Mombasa for clinker and fertiliser vessel offloading, handling and storage.
The company has also commissioned a train loading system in the port of Mombasa, linking all its Mombasa terminals with the terminals in Embakasi and Jinja. Clinker has traditionally been handled through conventional vessel operations, by using the vessel gears and sometimes shore-based mobile harbour cranes to offload the product onto tipper trucks before transporting the clinker to holding yards near the port area.
ACCOUNTABLITY MATTERS
Accountability is a crucial element of the GBHL business model.
During discharge, bulk cargo is weighed electronically in batches using shoreside scales at the quayside as it is conveyed to the silos and flat storage. This way, the rate of working can be monitored as well as the discharged quantity as the operation is in progress.
The final tonnage discharged can also be determined to facilitate immediate accounting of the actual quantity landed against the manifested tonnage. Government entities are also able to monitor the scales in real time.
Next, a printout of the progressive weighing is given to customs after the completion of discharge. The system ensures greater accuracy and reduced pilferage of bulk cargoes handled through the GBHL terminal as it is weighed on discharge, on bagging or delivery in bulk and at weighbridges, on road and rail, and on exiting the terminal.
Accountability in GBHL operations is a rule rather than an exception. This includes accountability in terms of the environment, a major ongoing focus point for the company.
The entire operation and systems employed by GBHL are environment and user-friendly, with all discharged cargo running through enclosed overhead discharge equipment and conveyors.
Before entering the silos, the cargo passes through dust extraction devices as a safety measure, and this is also repeated before deliveries. Dust emissions in GBHL’s operations remain at a minimum. GBHL operators recognise the need to protect the environment and maintain noise-free, dust-free and spillage-free handling systems.
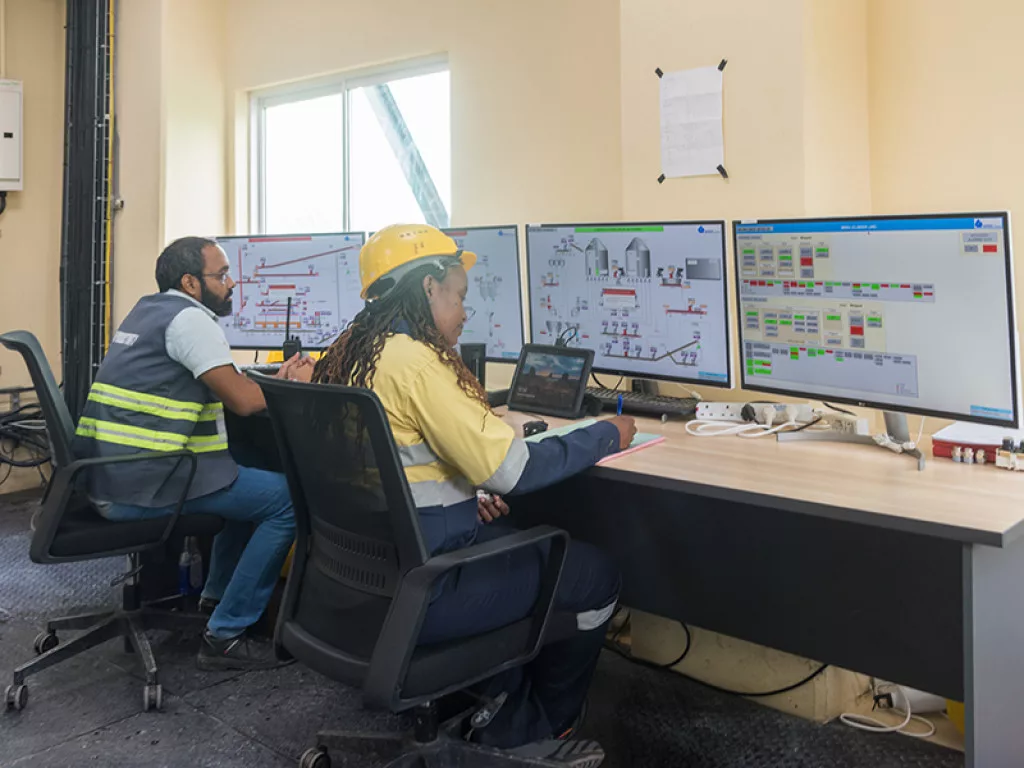
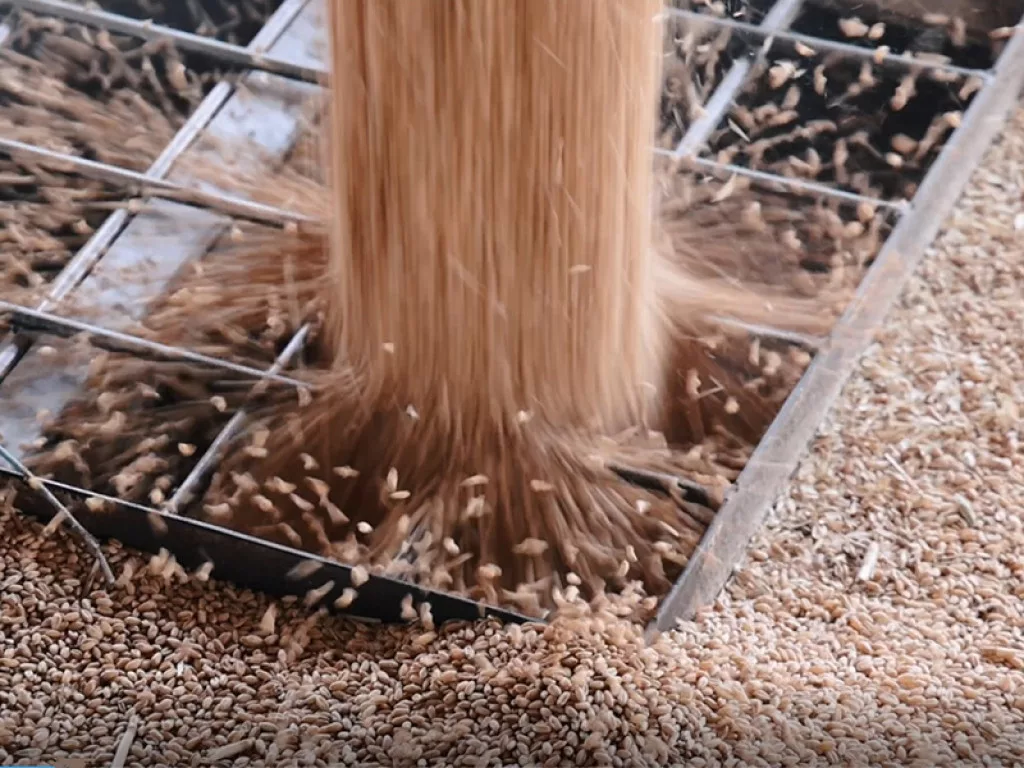
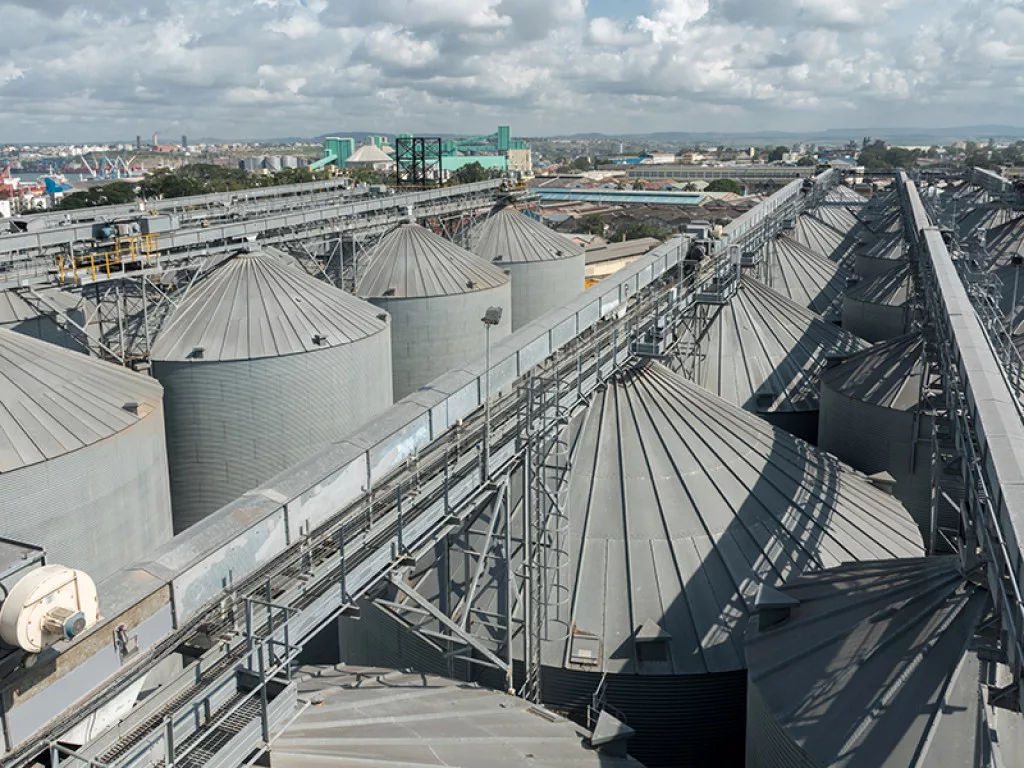
EXPANSION AND SUPPLY
GBHL has been working diligently to ensure that it has the right people, systems, processes and technology for sustainable operations in its existing businesses, along with the capacity to replicate that in new markets.
“As an organisation, we take pride in the achievements and progress we have made across the East African Corridor. We look forward to and welcome future opportunities in other countries and corridors throughout sub-Saharan Africa,” Locklear offers.
GBHL conducts complete due diligence and takes its time when finding new partners and suppliers for equipment across the supply chain which is vital when exploring these new opportunities, in order to secure the resources that the company needs to operate.
“Once we have found a partner or supplier that meets our criteria, we work diligently together to build a sustainable relationship that can be mutually beneficial and enables our business to operate efficiently 24-7, 365 days a year,” he continues.
“We must always meet our customers’ requirements every day, and thus it is critical that our service providers, partners and suppliers are also able to match those same obligations.”
AN ACCOMPLISHED TEAM
GBHL’s team remains extremely diverse, with most of its management and other members being Kenyan and Ugandan.
“We have staff that have studied all over the world with a broad spectrum of backgrounds and industry expertise. This diversity of experience ranges from port infrastructure development and operations to terminal management, financial analysts, engineers, automation specialists, logistics experts and even artificial intelligence designers,” Locklear reveals.
“Our expert team has been growing gradually over the course of our 22 years in operation, by bringing in new team members where required while also working diligently to internally promote and train our team members to grow within the organisation,” he adds.
Constantly scrutinising the market, GBHL ensures that its staff receive competitive remuneration and benefits, and can operate with a clear mindset knowing the company is looking after their best interests.
“We want to guarantee that our staff have the highest level of training to carry out their jobs at the peak level of performance and in the safest manner. We want our team members to all be leaders in their communities and within their individual families,” Locklear elaborates.
GBHL’s board of directors and senior management have committed to ensuring that in addition to the utilisation of technology, the company must have the best-skilled staff available. In order to achieve this, a robust training plan has been created that allows GBHL to continually improve its team’s capacity in their various roles, which will then lead to further promotions within the ranks.
“We have also created a graduate trainee programme where we work with a variety of top-tier universities and technical colleges in the region to attract the best talents, give them real-world experience, and then allow them to grow within our organisation. Ultimately, we are then able to hire exceptional full-time staff that are young, energetic, driven, and truly understand the business and our company culture,” he adds.
It is this trust in the process and the company’s people which has been proven to produce consistent results across every element of the business. The seamless development of all staff and attention to detail in GBHL’s training and market analysis ensure the future of the company looks brighter than ever.